Lean Manufacturing Principles - The Ultimate Guide
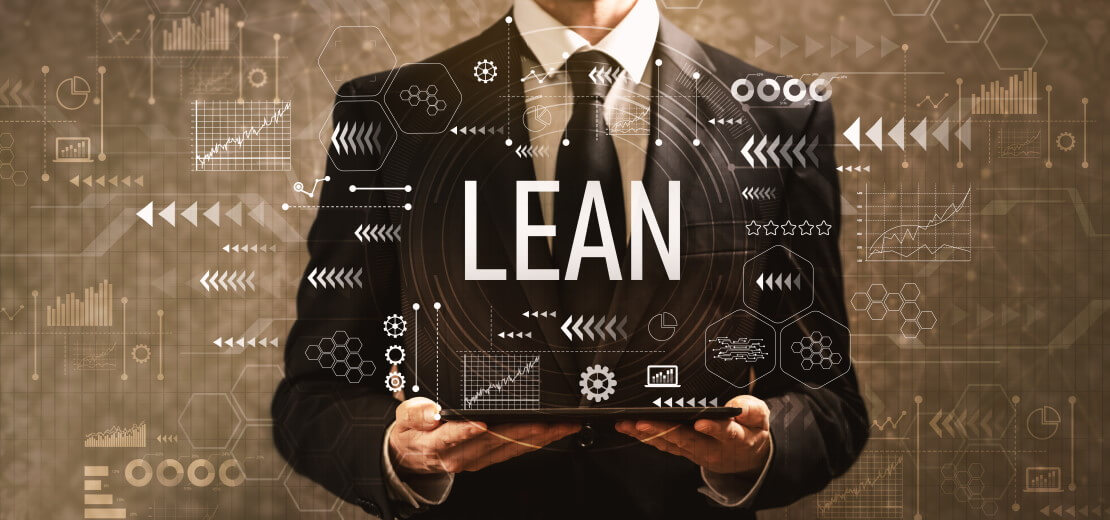
The main objective of Lean is to cut down on waste. Lean uses systematic techniques to accomplish this objective. Manufacturing is the traditional place to use Lean techniques, but you can also use them anywhere that you want to reduce waste.
Here is what we'll be covering in this guide to Lean:
1) Waste Elimination
Lean is all about eliminating waste. The reason it is called “lean” is because the objective is to have very “little waste.” Whenever you apply lean principles to manufacturing or anything else that you create, your goal should be to have little or no waste when you are done. If more businesses could create products while eliminating waste, it would do them a lot of good.
Here are how Lean techniques can help your business:
- Eliminate standing inventory to save on resources and space.
- Bring your workstations together to reduce the time of walking between them.
- Create usable by-products.
- Reduce production queues.
- Spread out workers to different tasks rather than having them do the same task.
- Increase process automation in the right areas.
As you can see, there are so many places where you can reduce waste in the workplace. By documenting your workflows, you can easily find the areas in your organization where waste can be eliminated.
You must manage your business processes to understand how well your workers are performing at their assigned tasks. Even if you know the proper way in which these tasks should be performed, it doesn’t mean you’ll know if your workers are following that method.
You cannot reduce waste if you have no idea how tasks are being performed in the workplace. So, make sure you understand how these tasks are being performed. It won’t eliminate all waste, but it will certainly help you improve your processes to eliminate more waste.
2) Kaizen - Continuous Improvement
It is not enough to reduce waste. You must make continuous enhancements to your processes to increase the performance. Then you can reduce more waste and prevent bottlenecks from getting in the way. If you find any inefficient processes, then you can work to make them better.
If you want to keep making things better in the workplace, then you must continuously improve all your procedures and practices. The first step is to manage your processes to determine where the biggest improvements need to be made. Once you find inefficiencies in certain areas of your processes, then you can reduce waste in those areas by improving the tasks related to them.
Do not expect to have good processes in the beginning. Most of you will probably have bad processes at first, and that is okay. All it means is you can continuously improve those processes and make them better from this point forward. Just remember to document your processes and ensure their accuracy.
A lot of beginners make the mistake of documenting how their processes “should be” rather than how they actually are. But you need to know the truth about your existing processes if you are ever going to improve them and make them better. The easiest way to achieve accuracy in your process documentation is to collaborate with employees. They can tell you what is really going on in the workplace because they see it every day. Then you can work to improve the areas with inefficiencies.
When you make a change to your process template in CheckFlow a new version is created for each change you make. You can view previous versions and revert back if required, thus providing full version control. This is a key requirement when practicing continuous improvement as it gives you the confidence to make changes without the risk of losing data or making a mistake. You can even duplicate your process templates and run multiple versions in parallel to compare the differences.
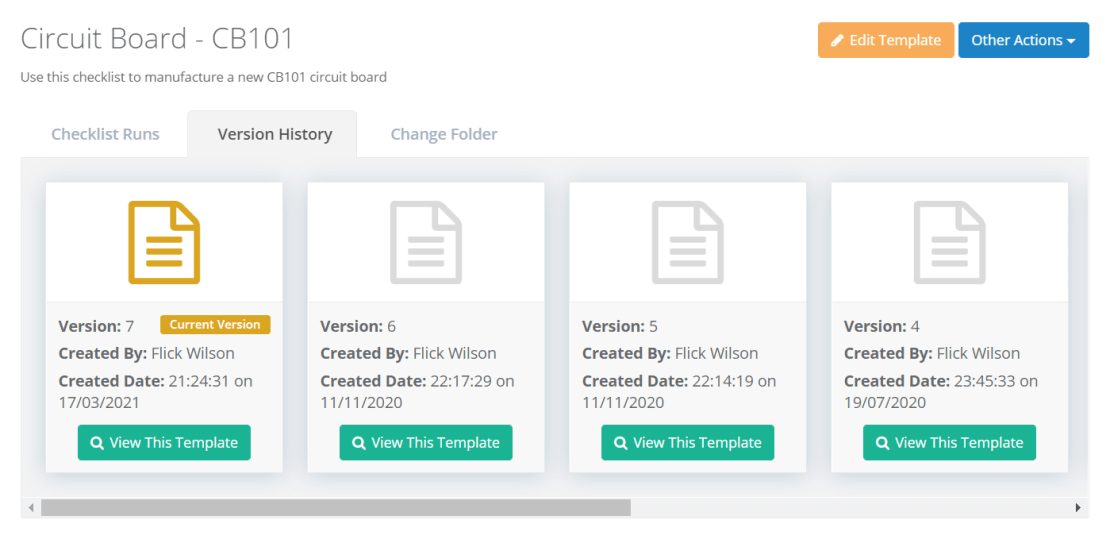
3) Value Your Employees
There are so many reasons to value your employees. The lean principles dictate that happy employees will be more engaged and productive in the workplace. Unfortunately, a lot of managers and business owners do not value their employees. They view them as expendable workers, which is why so many workers are disgruntled.
If you can learn to have a decent respect for humanity, then it will be easier to respect the people who work for you. That way, you can achieve high productivity and performance in your organization.
Here is how you can make employees happy:
- Make sure they understand the meaning and purpose of their work
- Do not work them to death
- Show how their personal goals coincide with the work they do.
- All successes and failures must have accountability.
- If there is a problem, have a polite conversation with your employee about it. Don’t assume anything until you’ve talked to them.
- Make sure nothing is in the way of your employees completing their tasks.
- It is okay to challenge your employees, but don’t make it sound like an order or demand.
- Give your employees different tasks to do, so their work doesn’t feel boring and repetitive.
All of this might sound simple, but it is never easy to manage human beings because they are not machines. They will always be unpredictable, which means you must rely on your communication skills to get through to them. If you can show a supportive attitude, then it will be easier to get them onboard with your company’s agenda.
Consistent and high-quality output will usually come from positive engagement with your employees. Then you can reduce human error because your employees will pay more attention to their work instead of zoning out and wishing they were someplace else.
4) Levelling Production
In lean manufacturing, the term “levelling production” means that you achieve the same output no matter what happens each day. Production consistency relies on you to review the average amount of orders you get per day. Then you won’t have to rush your production to fulfil the demand or end up with excess amounts of stock.
Of course, there will be times when you end up with more items than you sold. You don’t have to waste these items if they become fluctuation stock for your business. You never know when you’ll get an increase of orders again which will require you to tap into your fluctuation stock to fulfil them all.
To ensure your excess items get sold, you need to readjust your production rate and factor in your excess quantity of stock with the average order amount that you expect to have. Then you can match the number of orders received without having to produce too many new items.
You won’t be perfect at these calculations in the beginning. But as you gain more experience at levelling your production of items, your predictions and calculations will get easier.
If you’re making sophisticated products which take a while to create, then levelling the production is recommended. As long as you can predict the product demand well enough, then levelling production is highly effective. Fluctuation stock ensures you can fulfil orders without losing business over a lack of inventory. Then you won’t have to spend time rushing to produce a sophisticated product.
5) Just in Time Production
“Just in Time” production is a manufacturing principle for creating items or accomplishing tasks to fulfil current demands for them. There are no excess items or tasks in this principle. Therefore, there is no waste created here.
It is not easy to perform this principle because there are so many variables to influence the level of demand. But you’ll want to end up with no inventory in the end. This includes no finished products or raw resources left behind.
To pull this off properly, manufacturing managers must reorganize their processes to get everything just right. If they make bad predictions by underestimating or overestimating the level of demand, then it will increase waste or make them unable to fulfil orders.
Because of this, “Just in Time” is not a required principle to learn. It is better used by experienced managers who understand their workplace operations well and the level of demand to expect in a given day. If you cannot achieve “Just in Time” for the overall operation of your company, then apply it to individual tasks instead. It is easier to predict the outcome of smaller tasks than bigger objectives and goals.
The sophistication of your products and your ability to predict the demand for them are essential here. If you only have simple products to create, then it will be easier to produce them on demand. That will make it easier to follow the “Just in Time” principle. Otherwise, your customers will have to wait a longer time if you must create complex items on demand.
You won’t want to create too many of these products either under the “Just in Time” principle because they’ll remain as fluctuation stock for an indefinite time period. That does not reduce waste in the workplace.
6) One-piece Flow
One-piece flow takes your work-in-progress products and limits them to one item. This helps boost the quality and efficiency of the product after it is manufactured.
For example, let’s say you have many different workstations on the production line. When you get a bulk order, the one-piece flow means you move one item to the first workstation for it to be completely manufactured. After that, the completed item goes to the second workstation and the next product goes to the first workstation.
By arranging your production line in this manner, you will always have a product being manufactured during the process. There are no work-in-progress products waiting to be finished. You don’t have to travel very far between workstations either.
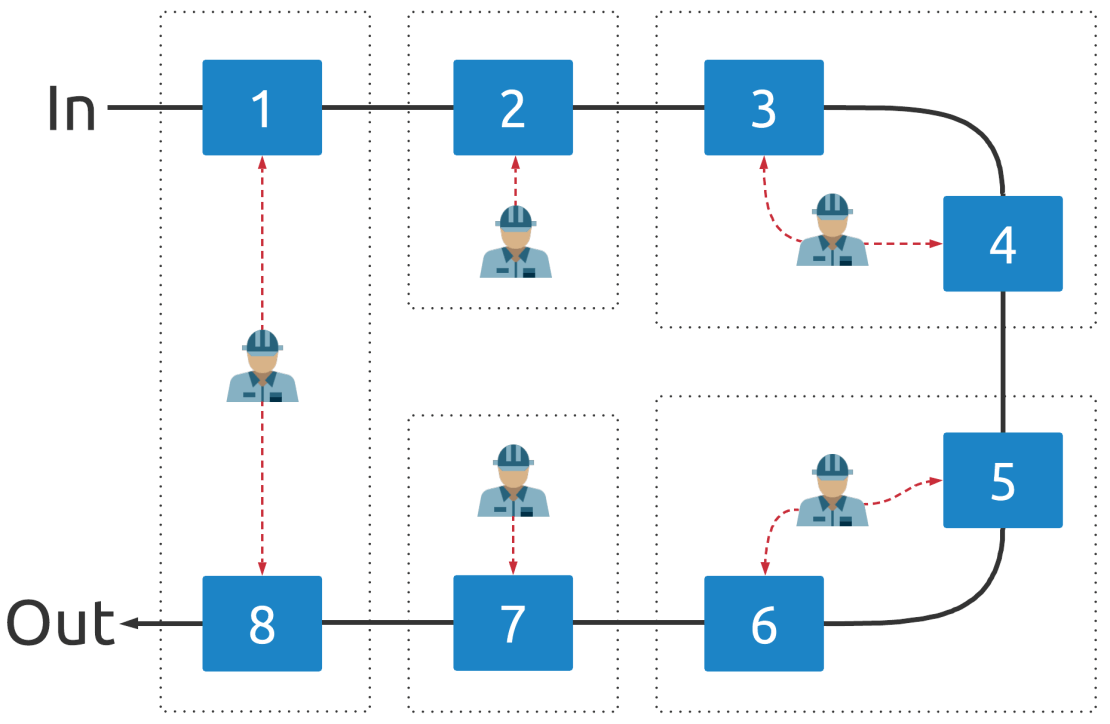
7) Quality
Every manufacturing process should put emphasis on creating high-quality products. That is how you achieve efficiency on the production line. Don’t try to create a bunch of cheap products quickly because they’ll end up with defects and problems that will ruin your reputation with consumers.
You may end up with low quality products because of human mistakes or bad processes. Use the following two lean techniques to increase the quality of your products:
- Poka-yoke to prevent mistakes in your manufacturing processes
- Jidoka to detect irregularities automatically
Always think about the value you are giving your customers. If you try to save efficiency on the production line, make sure you still have quality results in your products.
8) Poka-Yoke
Poka-yoke is a lean technique that focuses on developing quality products in manufacturing workflows. The technique focuses on designing your processes to prevent mistakes from being made along the way. This could involve the implementation of certain quality control measures or reengineering certain tasks to a new format that makes it easier to fix mistakes.
If you’re producing a massive number of items on your production line and want to discover errors, then you can use one of the following three types of poka-yoke to do so.
- Contact poka-yoke tests the physical attributes of products to identify defects in them.
- Fixed-value poka-yoke notifies the operator whenever a fixed number of movements do not occur.
- Motion-step poka-yoke notifies the operator whether certain predetermined steps have been followed or not.
Sometimes the poka-yoke device will automatically stop the mistake before it occurs. This is called a control poka-yoke. Otherwise, the operator will receive an alert notification about the mistake, which is known as a warning poka-yoke.
You can always expect some errors to be made in a manufacturing process. But if you can implement the proper poka-yokes, then you can catch the mistakes quickly and possibly stop more mistakes from causing defective products. Then you can save your business from losing consumer confidence and paying more money to replace their products.
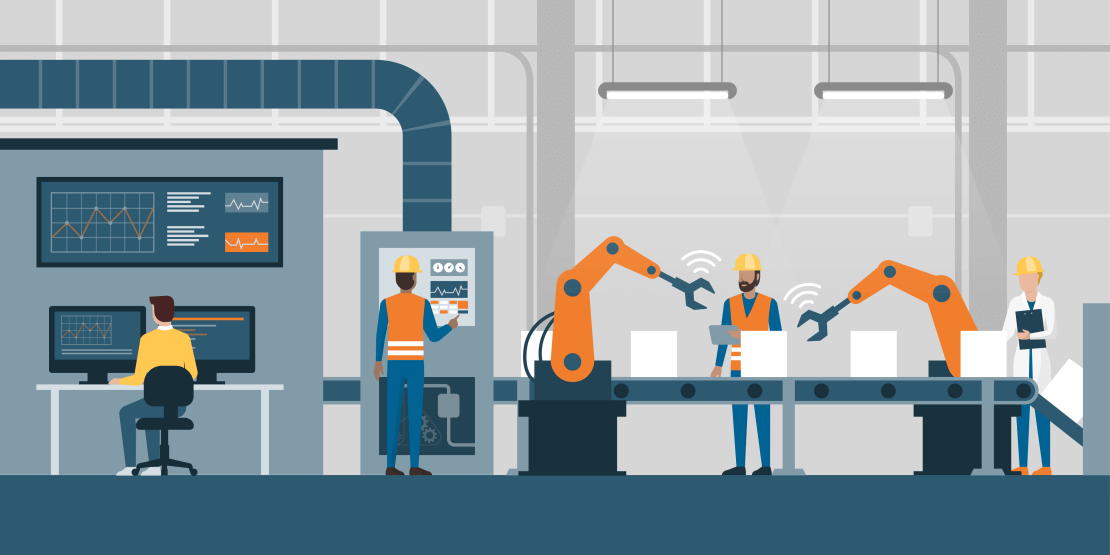
9) Jidoka
Jidoka utilizes automation to find defects in products. Then you don’t have to rely on human beings to discover the defects because human error is more common than automation error. Just set up a machine which is programmed to detect defects and errors automatically. If it finds an error, then it will sound off an alarm to notify you or your employees.
10) The Cycle of Lean Manufacturing
The cycle of lean manufacturing has five important steps to it. They can be applied as lean manufacturing principles too. The five steps are as follows:
- Identify Value - Figure out the value of your product to consumers
- Map the Value Stream - Figure out all the stages of your process and remove any stages which offer no value.
- Create Flow - Maintain a tight sequence when you create the workflow so that you can give the customer the most value at a fast speed.
- Establish Pull - Your customers should be demanding your product rather than you demanding for them to purchase your product.
- Seek Perfection - Always try to be perfect in the production process through continuous improvement, creating dependable processes, reducing/eliminating waste, and obeying all the lean principles that have been discussed.
Value for the customer is the main key. If you can remember that, then you are already on your way to making a more successful manufacturing business for yourself. The final result should always be a quality product for your customers.